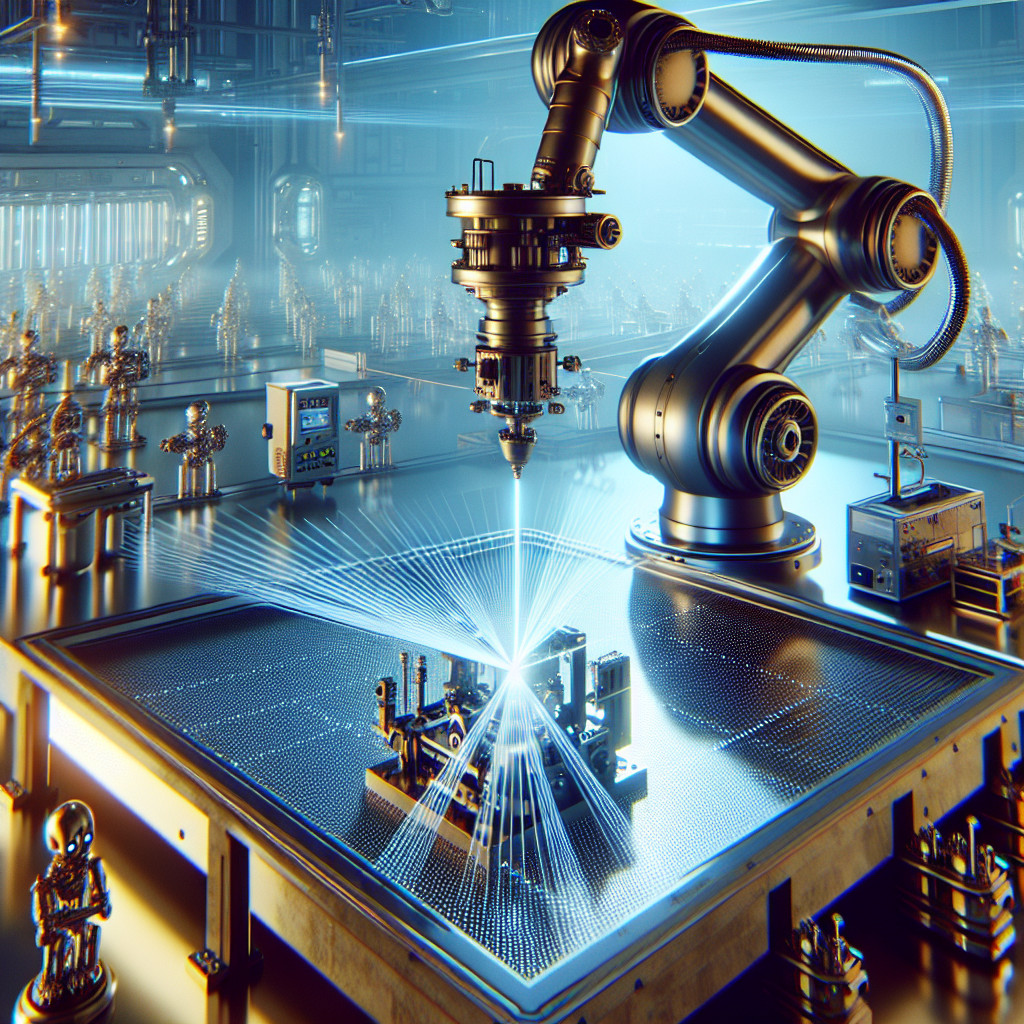
- Comparison of laser cleaning with traditional cleaning methods
- Applications of laser cleaning in various industries
- Limitations of laser cleaning for precision tasks
- Future developments in laser cleaning for precision tasks
- Challenges faced when implementing laser cleaning for precision tasks
- Training and certification requirements for operators of laser cleaning equipment
- Impact of laser cleaning on adhesion of coatings
- Role of laser cleaning in aerospace and automotive industries
Comparison of laser cleaning with traditional cleaning methods
Laser Cleaning
Laser cleaning is a non-contact method that uses a high-energy laser beam to remove contaminants from surfaces. The laser beam is directed at the surface, causing the contaminants to vaporize and be removed. This method is highly effective at removing stubborn contaminants such as rust, paint, and grease. It is also environmentally friendly as it does not require the use of chemicals.
Traditional Cleaning Methods
Traditional cleaning methods, on the other hand, involve the use of chemicals, abrasives, or mechanical tools to remove contaminants from surfaces. These methods can be effective, but they can also be time-consuming and labor-intensive. Additionally, they may not be as environmentally friendly as laser cleaning.
Comparison
Aspect | Laser Cleaning | Traditional Cleaning Methods |
---|---|---|
Effectiveness | Highly effective at removing stubborn contaminants | Can be effective, but may require more effort |
Environmental Impact | Environmentally friendly, does not require chemicals | May involve the use of chemicals that can be harmful |
Speed | Fast and efficient | May be slower and more labor-intensive |
Conclusion
In conclusion, laser cleaning is a highly effective and environmentally friendly method for removing contaminants from surfaces. While traditional cleaning methods can also be effective, they may not be as efficient or environmentally friendly. Ultimately, the choice between laser cleaning and traditional cleaning methods will depend on the specific needs of the cleaning task.
#laser #cleaning #traditional #methods #comparison #environmentallyfriendly #efficiency #contaminants
słowa kluczowe: laser, cleaning, traditional, methods, comparison, environmentally friendly, efficiency, contaminants
frazy kluczowe: comparison of laser cleaning, laser cleaning advantages, laser cleaning disadvantages, traditional cleaning methods, traditional cleaning effectiveness, environmental impact of cleaning methods, speed of cleaning methods.
Applications of laser cleaning in various industries
Automotive Industry
In the automotive industry, laser cleaning is used to remove rust, paint, and other contaminants from car bodies, engine parts, and other components. This process helps improve the quality of the surface preparation before painting or coating, resulting in better adhesion and longer-lasting finishes.
Application | Benefits |
---|---|
Rust removal | Improved surface quality |
Paint stripping | Enhanced adhesion |
Manufacturing Industry
In the manufacturing industry, laser cleaning is used for precision cleaning of metal parts, molds, and tools. This process helps maintain the quality and performance of the equipment, leading to increased productivity and reduced maintenance costs.
Application | Benefits |
---|---|
Mold cleaning | Improved product quality |
Tool maintenance | Extended tool life |
Electronics Industry
In the electronics industry, laser cleaning is used for removing oxides, residues, and contaminants from circuit boards, connectors, and other electronic components. This process helps ensure the reliability and performance of electronic devices.
Application | Benefits |
---|---|
Circuit board cleaning | Improved conductivity |
Connector cleaning | Enhanced signal transmission |
Conclusion
Laser cleaning is a versatile technology that offers numerous benefits in various industries. From automotive to manufacturing to electronics, laser cleaning is revolutionizing the way surfaces are prepared and maintained. Its efficiency, precision, and environmental friendliness make it a preferred choice for many applications.
#laser #cleaning #industries #automotive #manufacturing #electronics
#precision cleaning #surface preparation #environmental friendliness #rust removal #paint stripping #mold cleaning #tool maintenance #circuit board cleaning #connector cleaning
Limitations of laser cleaning for precision tasks
Another limitation of laser cleaning is the inability to remove certain types of contaminants. While lasers are effective at removing many types of contaminants, they may struggle with others such as rust or certain types of coatings. In these cases, alternative cleaning methods may need to be used in conjunction with laser cleaning.
Additionally, laser cleaning can be a time-consuming process. While it is efficient at removing contaminants, it may take longer than other methods such as chemical cleaning or abrasive blasting. This can be a drawback for tasks that require quick turnaround times.
Furthermore, laser cleaning can be expensive. The equipment and maintenance costs associated with laser cleaning can be high, making it a less cost-effective option for some applications.
In conclusion, while laser cleaning is a powerful and efficient method for removing contaminants from surfaces, it does have limitations that need to be considered for precision tasks. Damage to the surface, inability to remove certain contaminants, time-consuming process, and high costs are all factors that should be taken into account when deciding whether to use laser cleaning for a specific task.
#laser #cleaning #precision #limitations #surface #damage #contaminants #efficiency
frazy kluczowe:
– laser cleaning precision tasks limitations
– laser cleaning surface damage
– laser cleaning cost efficiency
– laser cleaning contaminants removal limitations
Future developments in laser cleaning for precision tasks
Another important advancement in laser cleaning technology is the integration of automation and robotics. By incorporating sensors and feedback systems, laser cleaning machines can adapt to changes in the surface condition in real-time, adjusting the cleaning parameters accordingly. This not only improves the efficiency of the cleaning process but also reduces the risk of human error and ensures consistent results across multiple tasks.
Furthermore, researchers are exploring new applications for laser cleaning technology, such as in the restoration of historical artifacts and the maintenance of critical components in aerospace and automotive industries. By harnessing the power of lasers, operators can achieve a level of precision and cleanliness that was previously unattainable with traditional cleaning methods.
In conclusion, the future of laser cleaning for precision tasks looks promising, with ongoing developments in technology and applications expanding the capabilities of this versatile tool. As researchers continue to push the boundaries of what is possible with laser cleaning, we can expect to see even greater advancements in the years to come.
Keywords: laser cleaning, precision tasks, technology, customization, automation, robotics, applications, restoration, maintenance, advancements
Long-tail phrases: laser cleaning technology advancements, precision laser cleaning applications, automated laser cleaning systems, laser cleaning for historical artifacts restoration, laser cleaning in aerospace maintenance.
#laser #cleaning #precision #technology #automation #applications #advancements #restoration #maintenance #robotics #customization #longtailphrases
Challenges faced when implementing laser cleaning for precision tasks
Another challenge is the complexity of the technology itself. Laser cleaning requires a high level of expertise and training to operate effectively. This can be a barrier for companies that do not have the resources to train their employees or hire skilled technicians.
Furthermore, safety concerns are a major challenge when it comes to implementing laser cleaning for precision tasks. Laser beams can be harmful to the eyes and skin, so proper safety measures must be in place to protect workers from potential injuries. This includes providing protective gear, implementing safety protocols, and ensuring that employees are properly trained on how to use the equipment safely.
In addition, the precision and accuracy of laser cleaning can also be a challenge. While laser technology is capable of removing contaminants with great precision, it can also be sensitive to factors such as surface material, thickness, and geometry. This means that the process may need to be adjusted or fine-tuned for different applications, which can be time-consuming and require additional resources.
Overall, implementing laser cleaning for precision tasks can be a complex and challenging process. However, with proper planning, training, and safety measures in place, companies can overcome these challenges and reap the benefits of this advanced technology.
#laser cleaning, precision tasks, challenges, technology, safety, cost, expertise, training, accuracy, efficiency
frazy kluczowe:
– laser cleaning for precision tasks challenges
– implementing laser cleaning technology
– precision tasks and safety concerns
– cost of laser cleaning equipment
– expertise and training for laser cleaning operations
Training and certification requirements for operators of laser cleaning equipment
Training Requirements
Operators of laser cleaning equipment must undergo comprehensive training to understand the technology, safety protocols, and proper operating procedures. The training program should cover the following topics:
- Basic principles of laser technology
- Safety precautions and regulations
- Equipment setup and calibration
- Material compatibility and surface preparation
- Maintenance and troubleshooting
Training can be provided by equipment manufacturers, industry associations, or specialized training centers. It is essential for operators to receive hands-on training to practice using the equipment under supervision before operating it independently.
Certification Requirements
After completing the training program, operators must pass a certification exam to demonstrate their knowledge and skills in operating laser cleaning equipment. Certification is typically valid for a certain period and may require renewal through additional training or exams.
Having a certification not only ensures that operators are competent in using the equipment but also provides credibility and recognition within the industry. Employers may require operators to be certified to comply with safety regulations and insurance requirements.
Conclusion
Training and certification are essential for operators of laser cleaning equipment to ensure safe and effective operation. By completing a comprehensive training program and obtaining certification, operators can demonstrate their proficiency and commitment to maintaining high standards in the industry.
#laser cleaning equipment, training requirements, certification requirements, safety protocols, operating procedures, hands-on training, certification exam, industry standards
frazy kluczowe:
– Importance of training and certification for laser cleaning equipment operators
– Safety measures and regulations for operating laser cleaning equipment
– Benefits of obtaining certification in laser cleaning technology
– Industry demand for trained and certified laser cleaning equipment operators
Impact of laser cleaning on adhesion of coatings
One of the key advantages of using laser cleaning for surface preparation is its ability to selectively remove contaminants without damaging the underlying substrate. Traditional methods of surface preparation, such as sandblasting or chemical cleaning, can be too aggressive and may cause damage to the surface, leading to poor adhesion of coatings. Laser cleaning, on the other hand, can be controlled with precision to remove only the contaminants while leaving the substrate intact.
Another benefit of laser cleaning is its ability to remove coatings without leaving behind any residue. Residue from old coatings can interfere with the adhesion of new coatings, leading to peeling or delamination over time. Laser cleaning completely removes the old coating, ensuring a clean surface for the new coating to bond to.
In conclusion, the impact of laser cleaning on the adhesion of coatings is overwhelmingly positive. By creating a clean, roughened surface that is free of contaminants and residue, laser cleaning improves the bonding strength of coatings and ensures a longer-lasting finish. As the technology continues to advance, we can expect to see even greater improvements in coating adhesion and overall surface preparation.
- Improved adhesion of coatings
- Clean and roughened surface
- Selective removal of contaminants
- No residue left behind
- #laser
- #cleaning
- #coatings
- #adhesion
long tail phrases: laser cleaning impact on coating adhesion, benefits of laser cleaning for surface preparation, improving bonding strength with laser cleaning
Role of laser cleaning in aerospace and automotive industries
W przemyśle lotniczym laserowe czyszczenie jest wykorzystywane do usuwania zanieczyszczeń z silników, skrzydeł, kabin, elementów podwozia i innych części samolotów. Dzięki precyzji i skuteczności laserów możliwe jest usunięcie nawet najtrudniejszych zanieczyszczeń, nie uszkadzając przy tym powierzchni. Ponadto laserowe czyszczenie jest bardziej ekologiczne niż tradycyjne metody czyszczenia, ponieważ nie wymaga użycia chemikaliów ani wody.
W przemyśle motoryzacyjnym laserowe czyszczenie jest wykorzystywane do usuwania zanieczyszczeń z karoserii, felg, silników, układów wydechowych i innych części pojazdów. Dzięki zastosowaniu laserów możliwe jest usunięcie farby, rdzy i innych substancji, nie uszkadzając przy tym powierzchni ani struktury materiału. Ponadto laserowe czyszczenie pozwala na oszczędność czasu i kosztów, ponieważ jest szybsze i bardziej efektywne niż tradycyjne metody czyszczenia.
W obu branżach laserowe czyszczenie ma wiele zalet, takich jak precyzja, skuteczność, ekologiczność, oszczędność czasu i kosztów. Dlatego coraz więcej firm z branży lotniczej i motoryzacyjnej decyduje się na inwestycje w technologię laserową. Dzięki laserom możliwe jest utrzymanie wysokiej jakości i wydajności produktów, co przekłada się na zadowolenie klientów i konkurencyjność na rynku.
Warto zauważyć, że laserowe czyszczenie ma również zastosowanie w innych branżach, takich jak przemysł elektroniczny, medyczny, spożywczy czy budowlany. Dzięki swoim zaletom laserowe czyszczenie staje się coraz bardziej popularne i powszechne w różnych dziedzinach przemysłu.
W podsumowaniu można stwierdzić, że rola laserowego czyszczenia w przemyśle lotniczym i motoryzacyjnym jest nie do przecenienia. Dzięki precyzji, skuteczności i ekologiczności laserów możliwe jest utrzymanie wysokiej jakości i wydajności produktów, co przekłada się na zadowolenie klientów i konkurencyjność firm. Dlatego warto inwestować w technologię laserową i wykorzystywać jej potencjał w różnych dziedzinach przemysłu.
#laser #czyszczenie #przemysł #lotniczy #motoryzacyjny #technologia #skuteczność #precyzja #ekologia #innowacje
frazy kluczowe:
– laserowe czyszczenie w przemyśle lotniczym
– zastosowanie laserów w przemyśle motoryzacyjnym
– zalety laserowego czyszczenia w różnych branżach
– inwestycje w technologię laserową
– rola laserów w utrzymaniu wysokiej jakości produktów
- Laser cleaning and long-term cost savings – cost analysis - February 29, 2024
- Laser cleaning and reducing emissions of harmful substances - February 28, 2024
- Can laser cleaning be used in veterinary medicine? - February 28, 2024