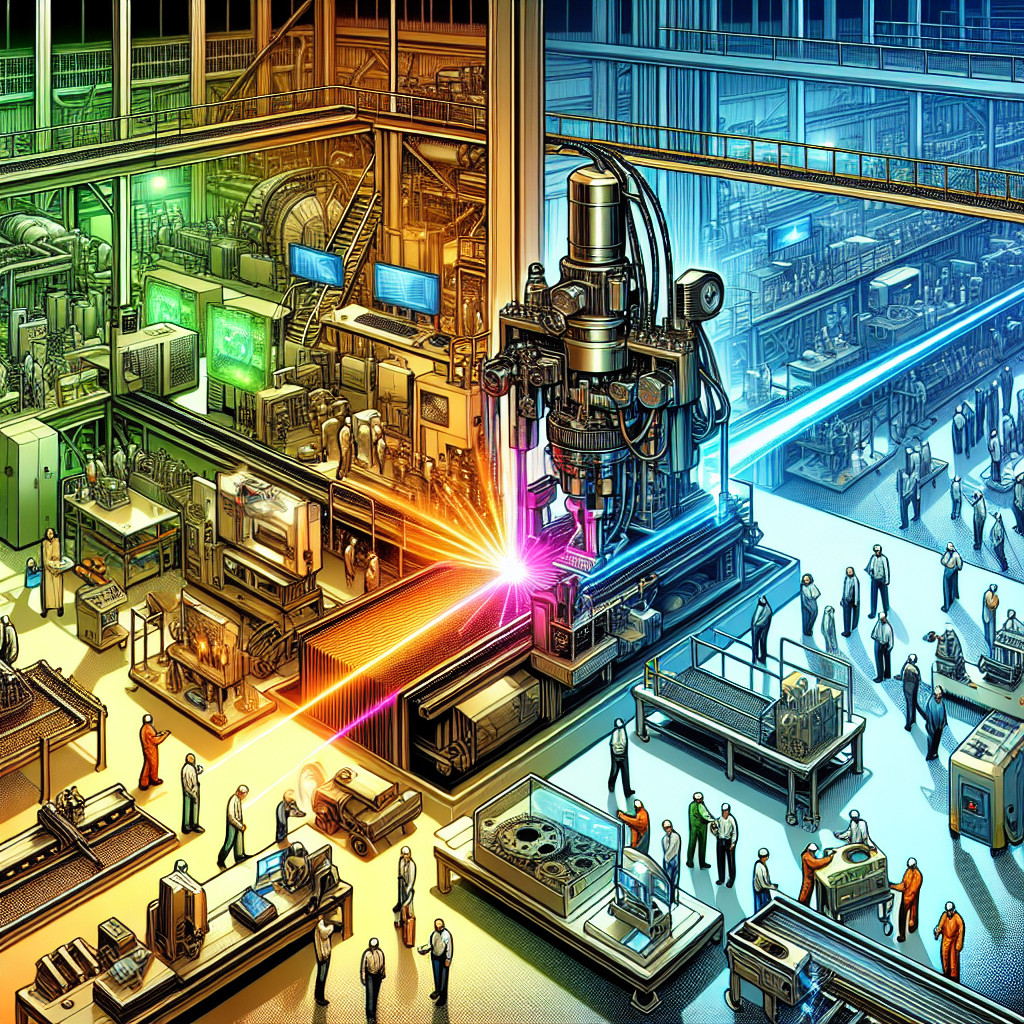
- Overview of laser cleaning technology
- Benefits of using laser cleaning in large-scale manufacturing processes
- Environmental impact of laser cleaning in large-scale manufacturing
- Comparison of different types of lasers used for cleaning
- Regulatory requirements for using laser cleaning in manufacturing
- Quality control measures for laser cleaning in manufacturing
- Impact of laser cleaning on product quality and performance
- Role of laser cleaning in achieving regulatory compliance in manufacturing
Overview of laser cleaning technology
Laser cleaning technology is a cutting-edge method used to remove contaminants, coatings, rust, and other unwanted materials from surfaces. This innovative technology utilizes high-powered lasers to vaporize or ablate the unwanted material, leaving behind a clean and pristine surface. Laser cleaning is a non-contact and environmentally friendly process that is increasingly being adopted in various industries for its efficiency and precision.
One of the key advantages of laser cleaning technology is its ability to selectively remove contaminants without damaging the underlying substrate. This makes it ideal for delicate surfaces or materials that cannot withstand traditional cleaning methods. Additionally, laser cleaning is a dry process, eliminating the need for chemicals or water, which reduces waste and environmental impact.
Laser cleaning technology can be used in a wide range of applications, including industrial cleaning, restoration of historical artifacts, and maintenance of machinery and equipment. In the industrial sector, laser cleaning is used to remove paint, rust, grease, and other contaminants from surfaces, preparing them for painting or welding. In the restoration field, laser cleaning is used to gently remove dirt and grime from delicate surfaces without causing damage.
The process of laser cleaning involves focusing a high-energy laser beam onto the surface to be cleaned. The laser energy is absorbed by the contaminants, causing them to vaporize or ablate. The resulting debris is then removed by a vacuum system or simply blown away by compressed air. The entire process is controlled by a computer system, which allows for precise control of the cleaning parameters.
In conclusion, laser cleaning technology is a versatile and efficient method for removing contaminants from surfaces. Its non-contact nature, precision, and environmental friendliness make it an attractive option for a wide range of applications. As technology continues to advance, laser cleaning is expected to become even more widespread in various industries.
- Efficient removal of contaminants
- Precision cleaning without damage
- Environmentally friendly process
- Wide range of applications
- Non-contact cleaning method
- Industrial cleaning
- Restoration of historical artifacts
- Maintenance of machinery and equipment
- Surface preparation for painting or welding
#laser #cleaning #technology
frazy kluczowe:
– Advanced laser cleaning technology
– Non-contact surface cleaning
– Precision removal of contaminants
– Environmentally friendly cleaning method
Benefits of using laser cleaning in large-scale manufacturing processes
Increased efficiency
One of the primary benefits of using laser cleaning in large-scale manufacturing processes is the significant increase in efficiency that it provides. Traditional cleaning methods often require time-consuming manual labor, chemical solvents, and abrasive materials. Laser cleaning, on the other hand, can be automated and completed in a fraction of the time, allowing manufacturers to streamline their production processes and reduce downtime.
Precision cleaning
Another key advantage of laser cleaning is its ability to achieve a level of precision that is simply not possible with traditional methods. The focused beam of the laser can target specific areas on a surface, removing contaminants without damaging the underlying material. This level of precision is essential for industries that require clean surfaces for optimal performance, such as electronics manufacturing or aerospace engineering.
Environmentally friendly
Laser cleaning is also a more environmentally friendly option compared to traditional cleaning methods. Because it does not require the use of harsh chemicals or abrasive materials, it produces less waste and reduces the risk of harmful pollutants being released into the environment. This makes laser cleaning a sustainable choice for manufacturers looking to reduce their carbon footprint and comply with strict environmental regulations.
Cost-effective
While the initial investment in laser cleaning equipment may be higher than traditional cleaning methods, the long-term cost savings can be significant. Laser cleaning is a more efficient process that requires less labor and materials, resulting in lower operating costs over time. Additionally, the precision of laser cleaning can help prevent costly damage to equipment or products, further reducing expenses for manufacturers.
Versatility
One of the most attractive features of laser cleaning is its versatility. It can be used on a wide range of materials, including metals, plastics, ceramics, and composites. This makes it an ideal solution for manufacturers working with diverse materials in large-scale production processes. Whether removing rust from metal surfaces or cleaning delicate electronic components, laser cleaning can adapt to the specific needs of any industry.
Conclusion
In conclusion, the benefits of using laser cleaning in large-scale manufacturing processes are clear. From increased efficiency and precision cleaning to environmental sustainability and cost savings, laser cleaning offers a range of advantages that can help manufacturers improve their production processes and stay ahead of the competition. By investing in laser cleaning technology, companies can achieve higher quality results, reduce downtime, and minimize their impact on the environment.
- Increased efficiency
- Precision cleaning
- Environmentally friendly
- Cost-effective
- Versatility
#laser #cleaning #manufacturing #efficiency #precision #environmentallyfriendly #costeffective #versatility
Environmental impact of laser cleaning in large-scale manufacturing
One of the main environmental concerns associated with laser cleaning is the generation of hazardous waste. When contaminants are removed from surfaces using lasers, they can become airborne and pose a risk to both workers and the surrounding environment. Additionally, the chemicals used in the cleaning process can be harmful if not properly disposed of.
Another environmental impact of laser cleaning is energy consumption. Laser cleaning requires a significant amount of energy to operate, which can contribute to greenhouse gas emissions and other forms of pollution. Additionally, the production of lasers and their components can also have a negative impact on the environment.
Despite these potential drawbacks, there are ways to mitigate the . For example, companies can invest in energy-efficient lasers and implement proper waste management practices to reduce the amount of hazardous waste generated. Additionally, using alternative cleaning methods, such as water-based or mechanical cleaning, can help minimize the environmental impact of laser cleaning.
In conclusion, while laser cleaning offers many benefits in large-scale manufacturing, it is important to consider the potential environmental impacts of this technology. By implementing sustainable practices and investing in environmentally-friendly solutions, companies can minimize the negative effects of laser cleaning on the environment.
Hashtags: #laser #cleaning #manufacturing #environmentalimpact
Keywords: laser cleaning, large-scale manufacturing, environmental impact, hazardous waste, energy consumption
Long-tail phrases: environmental concerns of laser cleaning, sustainable practices in manufacturing, minimizing hazardous waste in laser cleaning.
Comparison of different types of lasers used for cleaning
Laser Type | Wavelength | Power | Advantages | Disadvantages |
---|---|---|---|---|
CO2 Laser | 10.6 µm | High | Effective for organic materials | Not suitable for metals |
Nd:YAG Laser | 1064 nm | Medium | Versatile for various materials | Requires maintenance |
Fiber Laser | Various wavelengths | High | Precise and efficient cleaning | Expensive initial cost |
Each type of laser has its own unique characteristics that make it suitable for different cleaning applications. CO2 lasers are effective for organic materials, while Nd:YAG lasers are versatile for various materials. Fiber lasers offer precise and efficient cleaning, but come with a higher initial cost.
When choosing a laser for cleaning, it is important to consider the specific requirements of the application, such as the type of material being cleaned, the level of precision needed, and the budget available. By comparing the advantages and disadvantages of different types of lasers, you can select the most suitable option for your cleaning needs.
Overall, laser cleaning is a powerful technology that offers a non-contact and environmentally friendly solution for removing contaminants from surfaces. With the right choice of laser type, you can achieve efficient and effective cleaning results for a wide range of applications.
#laser #cleaning #technology #CO2 #NdYAG #Fiber #materials #precision #efficiency #environmentallyfriendly
frazy kluczowe:
– non-contact and environmentally friendly solution
– removing contaminants from surfaces
– efficient and effective cleaning results
– wide range of applications
Regulatory requirements for using laser cleaning in manufacturing
Here are some of the key :
1. Occupational Safety and Health Administration (OSHA) regulations: OSHA sets strict guidelines for the use of lasers in the workplace to ensure the safety of workers. Employers must provide proper training, protective equipment, and safety measures to prevent accidents and injuries.
2. Environmental Protection Agency (EPA) regulations: The EPA regulates the disposal of hazardous materials, including those generated during laser cleaning processes. Manufacturers must properly handle and dispose of waste to prevent environmental contamination.
3. Food and Drug Administration (FDA) regulations: If laser cleaning is used in the manufacturing of medical devices or pharmaceuticals, manufacturers must comply with FDA regulations to ensure product safety and efficacy.
4. International Organization for Standardization (ISO) standards: ISO has developed standards for laser safety, quality management, and environmental management that manufacturers must adhere to when using laser cleaning technology.
5. Local regulations: In addition to federal regulations, manufacturers must also comply with state and local regulations that may govern the use of lasers in manufacturing.
It is important for manufacturers to stay informed about regulatory requirements and ensure compliance to avoid costly consequences. By following these regulations, manufacturers can safely and effectively use laser cleaning technology in their manufacturing processes.
#regulatoryrequirements #lasercleaning #manufacturing #compliance
frazy kluczowe:
– Laser cleaning regulatory requirements in manufacturing
– Importance of compliance with laser cleaning regulations
– Ensuring safety and environmental protection in laser cleaning operations
Quality control measures for laser cleaning in manufacturing
Types of quality control measures
There are several quality control measures that can be implemented to ensure the effectiveness of laser cleaning in manufacturing. These measures include:
Measure | Description |
---|---|
Surface inspection | Before and after cleaning, surfaces should be inspected for any remaining contaminants or damage. |
Power and speed control | Monitoring and adjusting the power and speed of the laser to optimize cleaning efficiency. |
Monitoring debris | Collecting and analyzing debris generated during the cleaning process to ensure thorough cleaning. |
Temperature control | Monitoring and controlling the temperature of the surface being cleaned to prevent damage. |
Benefits of quality control measures
Implementing quality control measures for laser cleaning in manufacturing offers several benefits, including:
- Improved cleaning efficiency
- Reduced risk of damage to surfaces
- Consistent cleaning results
- Enhanced product quality
By implementing these measures, manufacturers can ensure that their laser cleaning processes are effective and reliable.
Conclusion
Quality control measures are essential for ensuring the effectiveness and reliability of laser cleaning in manufacturing. By implementing measures such as surface inspection, power and speed control, monitoring debris, and temperature control, manufacturers can achieve consistent and high-quality cleaning results.
#laser #cleaning #manufacturing #qualitycontrol #efficiency #precision #environmentalfriendly
słowa kluczowe: laser cleaning, manufacturing, quality control, efficiency, precision, environmental friendly
frazy kluczowe: quality control measures for laser cleaning, laser cleaning in manufacturing, laser cleaning benefits, laser cleaning efficiency, laser cleaning process.
Impact of laser cleaning on product quality and performance
Furthermore, laser cleaning enhances product performance by removing surface contaminants that can hinder functionality and durability. By eliminating residues and particles that can interfere with product operation, laser cleaning helps to optimize performance and extend the lifespan of products. This results in improved reliability and reduced maintenance costs over time.
Benefits of laser cleaning
- Efficient removal of contaminants
- Reduced risk of damage to surfaces
- Enhanced product quality and performance
- Cost-effective and environmentally friendly
In conclusion, the impact of laser cleaning on product quality and performance is undeniable. This advanced technology offers numerous benefits that contribute to the overall success of businesses in various industries. By investing in laser cleaning, companies can improve the cleanliness, efficiency, and longevity of their products, ultimately leading to greater customer satisfaction and profitability.
#laser #cleaning #productquality #performance #innovation #efficiency #precision #reliability #maintenancecosts
frazy kluczowe:
– Advanced technology for cleaning surfaces
– Improved product quality and performance
– Cost-effective solution for businesses
– Enhanced reliability and durability of products
– Environmentally friendly cleaning method
Role of laser cleaning in achieving regulatory compliance in manufacturing
One of the key benefits of laser cleaning is its ability to target specific areas without damaging the underlying material. This precision makes it ideal for removing contaminants from delicate components or hard-to-reach areas, ensuring that the finished product meets regulatory standards for cleanliness and safety.
By incorporating laser cleaning into their manufacturing processes, companies can improve the quality of their products while also reducing the risk of non-compliance with regulations. This proactive approach to regulatory compliance can help manufacturers avoid costly fines and legal action, as well as build trust with customers and regulators.
In addition to its environmental and safety benefits, laser cleaning also offers cost savings for manufacturers. By eliminating the need for harsh chemicals, abrasive materials, and manual labor, laser cleaning can reduce production costs and improve efficiency. This cost-effectiveness makes laser cleaning an attractive option for manufacturers looking to streamline their operations and stay competitive in the market.
Overall, the role of laser cleaning in achieving regulatory compliance in manufacturing cannot be overstated. By providing a safe, efficient, and environmentally friendly method of removing contaminants from surfaces, laser cleaning helps manufacturers meet regulatory standards while also improving product quality, reducing costs, and enhancing their reputation in the industry.
- Safe and efficient method of removing contaminants
- Environmentally friendly alternative to traditional cleaning methods
- Precision targeting for delicate components
- Cost savings and improved efficiency
- Regulatory compliance
- Laser cleaning
- Manufacturing industry
- Environmental impact
- Product quality
Hashtags: #regulatorycompliance #manufacturing #lasercleaning #environmentalimpact #productquality
Long-tail phrases: Role of laser cleaning in regulatory compliance, Laser cleaning for manufacturing industry, Benefits of laser cleaning in achieving compliance
- Laser cleaning and long-term cost savings – cost analysis - February 29, 2024
- Laser cleaning and reducing emissions of harmful substances - February 28, 2024
- Can laser cleaning be used in veterinary medicine? - February 28, 2024